The BMW Group is taking a forward-looking step with the Cell Manufacturing Competence Center in Parsdorf (CMCC). It is uniquely bundling the entire knowledge base for product and process.
A piece of the future has been under construction in Parsdorf since October 2023: 95 millimetres high, cylindrical and with a diameter of 46 millimetres. These are the battery cell designs that will be used in the Neue Klasse models from 2025 for the first time ever. They are manufactured in this new centre of excellence – the Cell Manufacturing Competence Center (CMCC) in Parsdorf. This is how the BMW Group is positioning itself efficiently to ramp-up electromobility and consolidating its leading role in battery cell technology.
“With the Cell Manufacturing Competence Center, we are strengthening Germany’s capacity for innovation,” explained Milan Nedeljković, member of the Board of Management of BMW AG, responsible for Production. “In this way, we are making an important contribution to the quantum leap in technology in the Neue Klasse.”
“Production of battery cell samples in Parsdorf marks the next logical step in our battery cell strategy,” said Frank Weber, member of the Board of Management of BMW AG, responsible for Development. “The Cell Manufacturing Competence Center is the perfect complement to our existing Battery Cell Competence Center in the north of Munich. Development takes place there, then we scale the best product towards a series process in Parsdorf. Thanks to cross-divisional collaboration, we are able to link product and process in a unique way.”
New format, new dimensions: the sixth generation is coming
The Parsdorf CMCC enables the BMW Group to fully demonstrate the cell’s value creation processes. This expertise enables the company to set benchmarks in production, quality, performance, costs and ecological standards together with its suppliers. Around 80 people are employed in the 15,000-square-metre CMCC. The current level of investment in the Cell Manufacturing Competence Center amounts to around 170 million euros. The Federal Ministry for Economic Affairs and Climate Action and the Bavarian Ministry of Economic Affairs, Regional Development and Energy are supporting the project under the auspices of the European funding process IPCEI (Important Projects of Common European Interest).
Recycling at the CMCC: keeping materials in circulation
Raw materials are one of the significant cost elements in cell production. The efficient and responsible use of source and carrier materials is therefore both prudent and necessary from an ecological and economic perspective. Experience is gathered in the new CMCC and findings progressed in all processes in order to further optimise the use of resources. This makes it possible to recover the residual materials generated during the production process in the CMCC, then sort and feed these back into the cell production cycle. As well as the manufacturing process of a cell, the BMW Group experts are also intensively involved in the reuse of materials and components of the entire battery after its initial use in the vehicle. The BMW Group has the long-term goal of the comprehensive reuse of raw materials used in recyclable high-voltage batteries.
This is how the cell is created: the production steps of the sample production at the CMCC
Cell production begins with the production of electrodes: here, the basic material, consisting of graphite and nickel oxides, among others, is dosed and mixed in a precisely measured ratio. This creates what is known as “slurry”. This is used to apply a wafer-thin coat to metal foils and then compress them. The technical jargon for this is “calendering”. It’s all about the highest level of precision: the film is only a few micrometres thick, thinner than the threads of a spider’s web. The newly cut foils, which are now called electrodes, are wound together in cell assembly with other subcomponents to form battery cells and inserted into the cell housing. The cells are filled with electrolyte in the formation, then charged and finally tested for quality.
The sixth generation of BMW battery technology: new cell format and advanced cell chemistry
The battery cell is fundamental to the central properties of e-vehicles: range, driving performance and charging time. The new BMW round battery cell, specially designed for the e-architecture of the Neue Klasse models, makes it possible to significantly increase the range by up to 30 per cent (according to WLTP) in the model with the longest range.
The new BMW round battery cells have a standardised diameter of 46 millimetres and two different heights of 95 millimetres and 120 millimetres. Compared to the prismatic cells of the fifth generation of BMW battery cells, the nickel content is increased on the cathode side and the cobalt content is reduced at the same time in the sixth generation BMW round cells. The silicon content is increased on the anode side. This results in the volumetric energy density in the cell being increased by more than 20 per cent.
The voltage of the energy storage, drive and charging technology of the Neue Klasse will increase to 800 volts. Among other things, this optimises the feeding of energy into fast DC charging stations. A significantly increased charging capacity can be achieved there with a current of up to 500 amps, meaning a reduction of up to 30 per cent in the time taken to charge from 10 to 80 per cent.
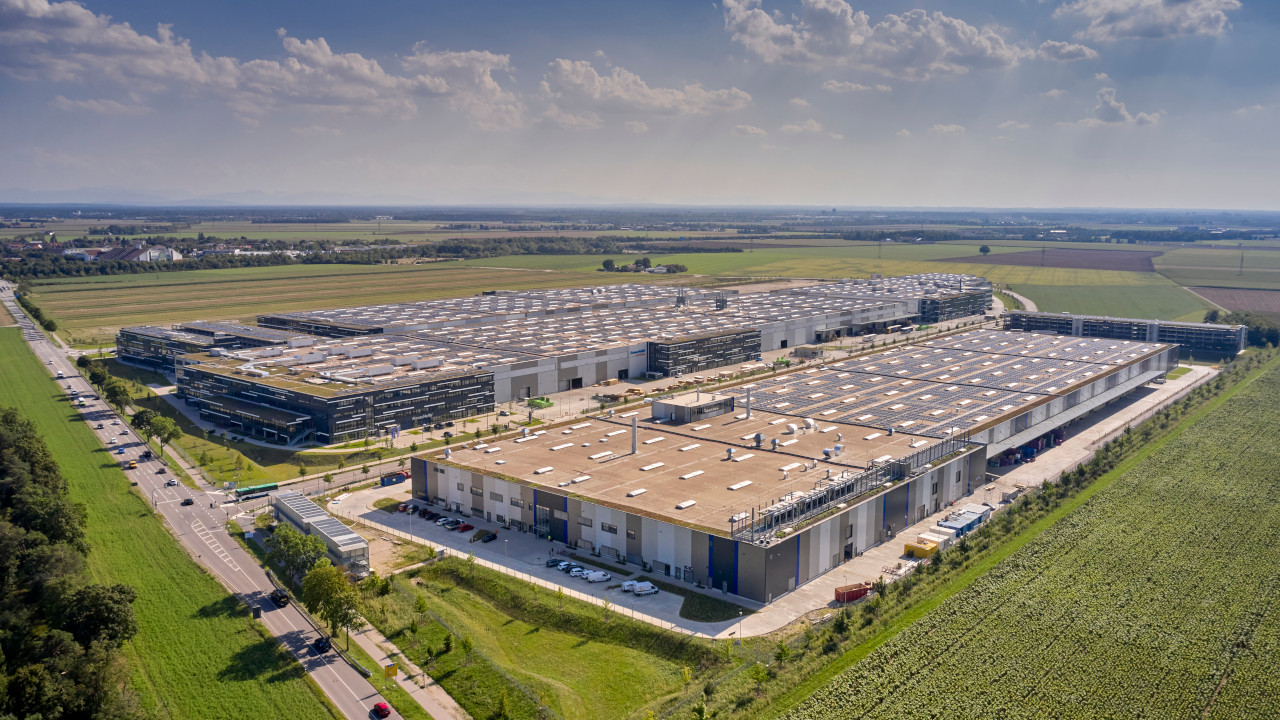